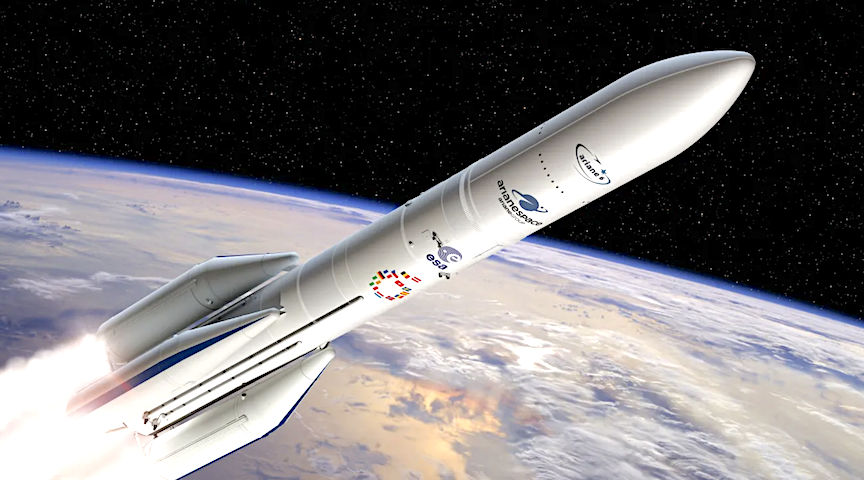
Beyond Gravity announces they will help shape the next generation of European launch vehicles: For the new Ariane 6 rocket, this global supplier for the space industry will provide the payload fairings. Just recently, the company, which has produced the payload fairings for all missions since Ariane’s first flight in 1979, successfully delivered the last structures from Emmen (Switzerland) for its predecessor, Ariane 5.
André Wall, CEO of Beyond Gravity said, “We are proud to have been a close partner to ArianeGroup for decades and to continue our joint success story also for the next generation of launch vehicles. Over the years, Beyond Gravity has manufactured more than 250 payload fairings for the Ariane launcher rockets and was instrumental in the development of the new payload fairing for Ariane 6.”
“This contract with Beyond Gravity is a new and key step towards a strong Ariane 6 European team” said Stephane Nogatchewsky, EVP Head of Procurement, ArianeGroup. “While the inaugural flight of Ariane 6 is getting closer and the industrial ramp up is intensifying, this collaboration is a positive and critical milestone for the future of Ariane 6 operations. Also, unifying European actors is paramount to ensure further A6 industrial robustness, competitiveness and preserve European autonomous access to space.”
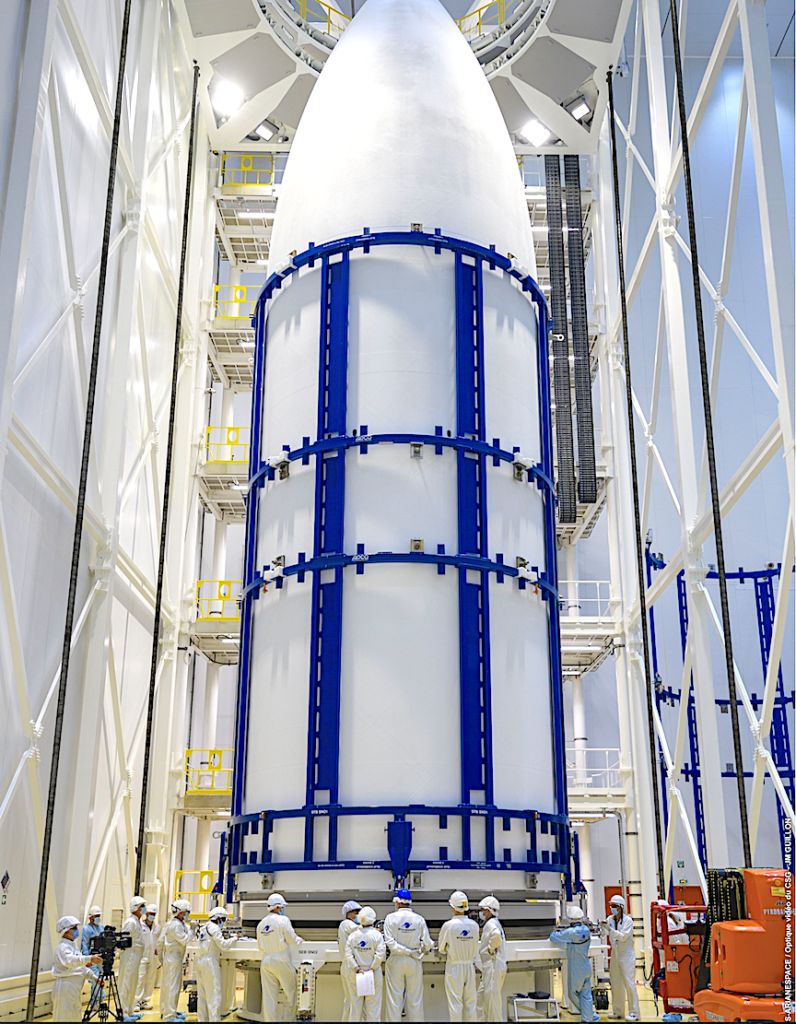
The two variants of the Beyond Gravity Payload Fairing offer two different sizes and consist of two half-shells that separate once they reach orbit. Accounting for one third of a launch vehicle’s total length and rising to the height of a six-story building, the 20 meters high larger variant (A64) safeguards the valuable cargo on its voyage to space. The smaller version is 14 meters high. Both versions have a 5.4-meter diameter, ensuring ample room for a variety of payloads. Thanks to the advanced carbon fiber composite design, the structure weighs only 1.8 to 2.6 tons and is therefore featherweight and stable at the same time.
“Rooted in a legacy of incremental innovation, our payload fairings are a testament to the strength, efficiency, and progressive ingenuity we continue to nurture at Beyond Gravity,” states Paul Horstink, Executive Vice President. “Our payload fairings stand as a formidable structure today, but we’re not stopping there. Especially with the commercial market in mind, we are driving future innovations, such as further shortening lead times or exploring possibilities in reusability to redefine the boundaries of space exploration.”
In technical terminology, the rocket tops are called “payload fairings”. Their main task is to protect the satellites from high temperatures, solar radiation, dust, moisture or rain at the launch site before launch. In the first minutes of flight, it is primarily the noise, the enormous frictional heat and the mechanical stresses from which the payload fairings reliably protect the satellites encapsulated beneath them. In a semi-automated process, Beyond Gravity manufactures each half-shell in one piece from carbon fiber composite material that is “cured” in an industrial oven without the use of an autoclave. This reduces costs and speeds up production.